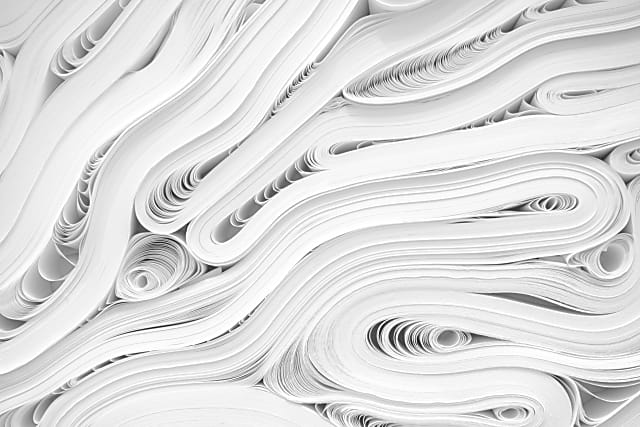
White papers
Stay up to date on the latest topics and gain industry insights from HMS' experts through our white papers, providing valuable knowledge and analysis.
IAS Inc., an automation engineering company, partners with Ewon to provide remote monitoring and troubleshooting services, enhancing customer support, saving costs, and maximizing up-time.
Nestled away in a non-descript suburban Milwaukee business park lies an Engineering and Integration company with a worldwide shadow. Founded in 1998, IAS Inc. of New Berlin Wisconsin has grown from humble beginnings to a leading authority in the automation fields of robotics, machine vision, and motion control.
With clients cast far afield, IAS’s President and Founder, Paul Szeflinski has been a proponent of remote monitoring of control systems for a very long while.
Quoting Mr. Szeflinski: “We saw the value of remote work on our systems many years ago. Over the years we’ve tried almost everything, including some systems which required ‘IT Wizardry’ and lots of phone time with the IT department of our clients. But just about the time the client needed our assistance, we discovered the system had been changed and we couldn’t access the equipment.”
Today we offer the ability to retrofit an older system with Ewon.
Paul Szelfinski, President, IAS Inc.
The local automation distributor brought in a solution which combines unique gateway capability with a SaaS tool to enable safe communications from Ewon. Skeptical at first, IAS went through rigorous testing prior to placing the device into a customer installation. Again quoting Mr. Szeflinski, “Our first live application was a robotic system with a PLC based conveyance system. It was a complex system with PLCs communicating with drives, HMIs and tons of other equipment and we wanted the customer’s experience to be absolutely flawless.” IAS employed Ewon’s system and discovered they could impact the customer’s up-time in a massive way.
After such positive customer feedback IAS Inc. began offering Ewon devices in each new system design. Along the way they have pushed the solution in new and innovative ways. “We have connected to vision systems, which enabled us to capture images remotely. This allowed us to diagnose issues and refine parameter limits to improve the reliability of the inspection.”
Using Ewon’s unique strategy for accessing remote equipment has saved IAS customers tens of thousands of dollars. And the benefits are not only for international customers: “A client operating a state of the art printing facility a couple of states away had a system issue which brought their thousand dollar an hour press to a screeching halt. Troubleshooting via the Ewon gateway and Talk2m, we discovered a faulty Ethernet cable on the machine and got them running in less than two minutes.” Imagine the up-time benefit to the customer.
If a machine stops running, IAS Inc. is able to remotely troubleshoot it within a few minutes.
Automation customers value up-time. A fully automated plant that isn’t running is a drag – a drag on morale, a drag on profits and an issue that impacts the plant’s customers. Seeing the massive customer benefit sparked an idea with Paul and his management team. Why not offer remote monitoring and troubleshooting as a service? “After sharing the experience of remote troubleshooting with customers who have purchased machines from us in the past couple of years, we decided to push the model forward. Today we offer the ability to retrofit an older system with Ewon to take advantage of this great technology. We charge a modest fee for our team to be ready to jump in when the machines go down. And, our customers have responded very positively. As a matter of fact, several have asked us to take over the troubleshooting of equipment purchased from others. We are honored to be able to assist,” says Paul.
We are on the cusp of a new industrial age. One of the principle drivers of this IIoT (Industrial Internet of Things) is the maximization of engineering resources. Ewon is the IIoT we can launch today. Systems Integrators like IAS Inc. have developed incredible engineering resources along with the proper tools and software to quickly effect needed changes in an industrial automation environment. End users of the equipment get greater productivity and enhanced profits by eliminating rejects, waste and lost employee hours. IAS Inc. and a cadre of other progressive engineering teams are in the vanguard of this movement and Ewon is their tool.
Stay up to date on the latest topics and gain industry insights from HMS' experts through our white papers, providing valuable knowledge and analysis.
Our products solve everyday industrial communication problems. Discover how our customers have improved their business with HMS case studies.
HMS communication solutions help thousands of companies solve specific communication problems in many different industries and applications.