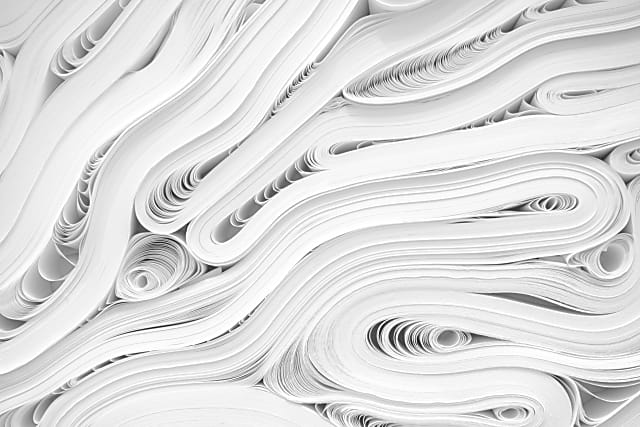
White papers
Stay up to date on the latest topics and gain industry insights from HMS' experts through our white papers, providing valuable knowledge and analysis.
CODIMAG improved productivity and reduced maintenance costs by implementing the Ewon remote access system. This solution allows remote monitoring and troubleshooting, benefiting both customers and engineers.
CODIMAG, a renowned label printing machine provider, shares with us how they add value to their service with Ewon remote access solution.
Based in Bondoufle, France, CODIMAG has devoted the past four decades to developing the finest label printing machines in the world. Using a combination of their own Aniflo press technology along with complex motion and automation control components, CODIMAG has been recognized as the state-of-the-art in the label printing business not only in their native France but around the world with more than 400 machines placed on all continents.
By remotely monitoring their machines with the Ewon remote access solution, CODIMAG was able to increase productivity and uptime for their customers, while cutting in maintenance costs.
Since unplanned production downtime certainly costs machine builders money, efficiently maintaining their machine performance from overseas was a real challenge for CODIMAG. Often the customer needs their idle machine fixed as soon as humanly possible. This results in high urgent travel costs that could amount to over USD$ 4,000, even for a short trip. While the engineers are away, new projects at CODIMAG are delayed and new designs postponed because it’s difficult to get real work done while traveling. Not only their customers face production delays, but CODIMAG also struggles to improve engineer engagement, as the engineers are forced to miss their children’s soccer games, family gatherings, and sometimes miss out on holidays. Companies, like CODIMAG, with small teams find themselves scrambling to find new and qualified professionals just in case they have field issues.
CODIMAG needed to look for a solution that can help them improve productivity for their customers and their engineering team efficiency.
CODIMAG began applying the Ewon remote access solution with a machine installed in Brazil in 2011.
“Because of the distance associated with this project, we decided we could provide better and more cost-effective service to our customer by installing the Ewon device to the automation side of our press. This allowed us to understand all the issues with the press without booking a flight and heading to South America.
The customer enjoyed more productivity and uptime; we found ourselves making fewer service trips.
Benoit Demol, CEO, CODIMAG
Remote access of equipment in the field has long been the dream of automation professionals. Until now issues with speed, reliability of connection and security put this dream just out of reach, but Ewon’s unique product solves those issues. Using the internet and a fully secure SSL-based VPN tunnel for all traffic. The information exchanged during the communication is encrypted via SSL (2048-bit key) allowing only authenticated users to connect. Ewon’s free cloud service Talk2m uses a managed, hybrid, layered cyber security approach to protect its devices and network. But most importantly, this system protects the customers’ internal network from malicious attacks on their industrial systems.
Applying Ewon has been a win-win situation for CODIMAG and customers alike. Their customers get improved productivity and more cost-effective operation. When visits are required, both benefit from CODIMAG’s ability to pre-access part failure.
The first experience with the system in Brazil impressed CODIMAG enough for them to make the decision to provide a Ewon gateway with every machine sent to the field. “Even if the press is only 200 kilometers (125 miles) away, it still improves the customer’s productivity to have instant access to the automation controls,” Demol explained.
The Ewon gateways are easy to use. Most engineers can get a system up and running the first time in less than 20 minutes. Gathering detailed information remotely allows the CODIMAG support team to solve the issue 80 percent of the time in a matter of minutes rather than days without the expense associated with a trip.
When a trip is necessary the engineer knows what parts will be needed to make the repair before leaving their office. This point makes the trip shorter by eliminating the waiting time required for parts to be air freighted to the customer location. The net result is speedier return to productive service and less burden on the CODIMAG’s small engineering team. When the machine works well, the customer prints more labels and the engineering team is less distracted.
Stay up to date on the latest topics and gain industry insights from HMS' experts through our white papers, providing valuable knowledge and analysis.
Our products solve everyday industrial communication problems. Discover how our customers have improved their business with HMS case studies.
HMS communication solutions help thousands of companies solve specific communication problems in many different industries and applications.