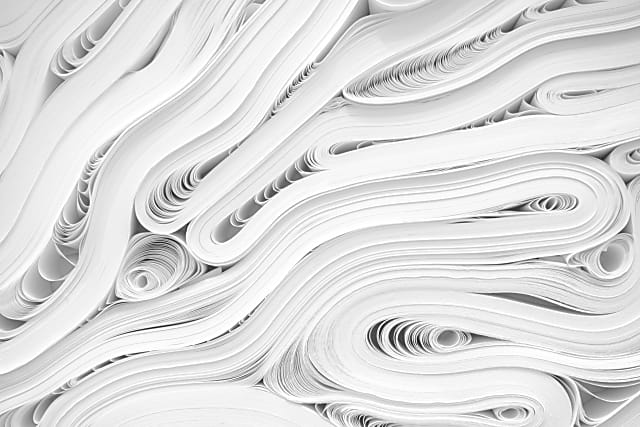
White papers
Stay up to date on the latest topics and gain industry insights from HMS' experts through our white papers, providing valuable knowledge and analysis.
Atlas Copco improved semi-manual screwdriving efficiency and safety by using Ixxat Safe T100 I/O modules and Anybus modules, reducing cables and enhancing flexibility and diagnostics in automotive assembly processes.
In the automotive industry, precise and reliable screwdriving processes are essential, especially when assembling engines and bodies. Atlas Copco, a manufacturer of automated screwdriving solutions tasked with this was confronted with the challenge of designing semi-manual screwdriving processes to be more efficient and safer. In the process, several servomotor are used to operate a tool in order to tighten screws with a precisely defined torque in a specific order, for example for the final assembly of wheels. Since the tool is also guided manually, it must be possible at all times to safely shut down the torque locally. The screwdriving processes are controlled by a programmable logic controller (PLC) while the worker only guides the tool and starts the screwdriving process. Alternatively, the screwdriver can also be mounted on a robot arm for fully automated operation.
The existing solution for worker guidance caused too high of a weight as well as restricted flexibility with the screwdriver control due to the existing cable routing. The controllers have to ultimately be flexibly expandable to be able to adapt to different numbers of screws. Another challenge was reliably shutting down the screwdriver motors either individually or in combination, since the current daisy chain configuration in the emergency stop circuit only allowed for all devices to be shut down. This led to unnecessary production interruptions and potential safety risks.
The solution to this challenge was implementing the Ixxat Safe T100 I/O modules from HMS Networks, which were used in combination with Anybus CompactCom modules. This solution made it possible to communicate via the fieldbus instead of fixed wiring. The local emergency stop could now be transmitted via the fieldbus to the respective servo controllers, which reduced the number of cables and the associated errors, and also improved the diagnostic possibilities.
Thanks to the modular approach with the T100 module and the CompactCom module, the safety via fieldbus remained an optional customer solution. The expandability was simplified, since no additional safety cables had to be laid. A defined shutdown of connected motor controllers was realized via the safety PLC, without requiring physical rewiring. Emergency stop groups could be configured in the safe application. Using the Anybus CompactCom and the Ixxat Safe T100 module made it possible to connect the screwdriver servos to the controllers of different manufacturers (Siemens, Rockwell, Beckhoff), whereby the safe/non-safe protocols could be easily interchanged.
The Ixxat Safe T100 module is a pre-configured safety module that allows for seamless functional safety implementation into industrial applications. It offers a flexible safety solution, which can be used both in individual applications, as well as in complex production environments. The combination with Anybus CompactCom modules allows for safe and efficient fieldbus communication.
Company: Atlas Copco
Solution: Functional safety implementation
Industries: Production automation, automotive industry
Products: Ixxat Safe T100 I/O module with Anybus CompactCom module
Stay up to date on the latest topics and gain industry insights from HMS' experts through our white papers, providing valuable knowledge and analysis.
Our products solve everyday industrial communication problems. Discover how our customers have improved their business with HMS case studies.
HMS communication solutions help thousands of companies solve specific communication problems in many different industries and applications.