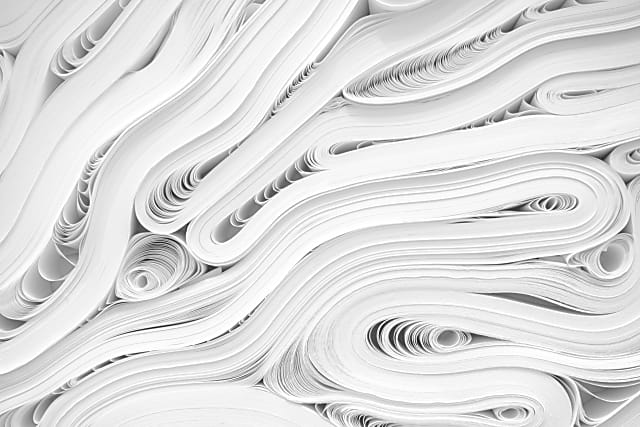
White papers
Stay up to date on the latest topics and gain industry insights from HMS' experts through our white papers, providing valuable knowledge and analysis.
Discover how Bosch’s partnership with HMS Networks continues to thrive and how Anybus Gateways enhance security
Bosch Industriekessel GmbH, a company of the Bosch Home Comfort Group, has been making industrial boilers since 1865, specializing in producing steam and hot water boilers, including large-scale units that generate up to 55 metric tons of steam per hour.
Klaus-Hinrich Koch, Development Engineer, highlights Bosch’s enduring expertise:
“We’ve been making industrial boilers for a long time and now stand as market leaders
in our segment.”
A key factor in Bosch’s success is their ability to evolve with the times, offering modern
solutions such remote management of boilers and a range of decarbonized, electrical
boilers. Klaus provides a good example. “We recently worked with a fish factory in
Iceland where they produce their own packaging material using steam from one of our
electrical boilers, powered by 100% green electricity.”
Bosch’s partnership with HMS began in 2011 when Bosch started to include Anybus X-Gateways with their Boiler Control (BCO) and System Control (SCO) systems. The BCO manages the boiler itself, while the SCO oversees the entire boiler house, automating systems like feed water conditioning, condensate return, fuel monitoring, and more.
Klaus explains the setup: “For a typical installation with two boilers, each boiler has its own BCO, with a dedicated connection to the SCADA system. Additionally, the SCO manages the overarching systems and is also connected to the SCADA system. In this scenario, we use three Anybus gateways—one for each BCO and one for the SCO.” The Anybus gateways play a critical role in ensuring connectivity. “If a customer wants data from our boiler system, we use an Anybus gateway to connect their SCADA system to our BCO or SCO. Our systems use PROFINET, but the customer might use Modbus TCP, RTU, or PROFIBUS, and then we use the gateway to convert the protocols,” Klaus explains.
But the gateways don’t just offer protocol conversion, they also enhance security. “For maximum security of our systems, it is important to decouple system control from data communication. This helps avoid security-critical misuse from outside the system while maximizing the seamless integration of data into the local automation system. That is why we still use a gateway even if the customer uses PROFINET. For security reasons, we have to separate the boiler house network from the customers network”.
To simplify the installation at the customer site, Bosch
preconfigures the gateways for their side and, if provided with
the necessary information, also for the customer side before
shipping. They also conduct comprehensive testing before
anything leaves the factory. “We want to spot and resolve
problems before we deliver anything. Trying to solve issues
later is very time-consuming and expensive,” explains Klaus.
Cutting-edge boilers require cutting-edge gateways, which is why Bosch is currently transitioning from the Anybus X-Gateways to the next generation Anybus Communicators. “We’ve delivered some boiler systems with the new Modbus TCP to PROFINET and PROFIBUS to PROFINET Communicators, and we’re waiting for the PROFINET to PROFINET Communicators [Editor’s note- it’s coming, to be released in fall 2024!].”
To support the transition from Anybus X-Gateways to Anybus
Communicators, HMS provides a legacy mode which has
been a great help to Klaus and his team. “Legacy mode is
very important for us because it allows us to switch to the
Communicator without changing the configuration or
the Communicator without changing the configuration or
programming”.
Bosch has noticed and appreciated several improvements in the new Anybus gateways, including enhanced usability, accessibility, and cybersecurity. “The web-based user interface makes configuration easy. It’s quicker to install and also easier to understand. This is good for us and our customers. We also use the diagnostics tab in our test system to check the connections during our integration tests. It’s good as we can easily see if the data is being transmitted correctly.”
The ability to configure the Communicator via the web interface has also helped. “The Ethernet connection is useful. I can put the Communicator in the same address range as our PLC, program our PLC, and see the connection on the Communicator’s webpage. It’s easier because I don’t have to change addresses.”
The security enhancements in the Communicator have also impressed. “Cybersecurity is becoming increasingly important, and the Communicator helps us improve security. It provides an extra layer of security by segmenting the network, but it also includes some nice security features. I particularly like the security switch, the little switch on the Communicator. It’s good as it prevents changes to parameters, addresses, and so on, in an easy way. During our testing process, we performed some hacking tests, and the Communicator passed them all. It was not possible to access our PLC from the customer’s side of the network, so the security features worked well”.
In the Anybus Product Emulator you can browse the intuitive user interface to get a look and feel of the configuration interface. It’s even possible to prepare configurations files without any product connected to your computer.
Learn more at www.hms-networks.com/anybus and www.bosch-industrial.com
Stay up to date on the latest topics and gain industry insights from HMS' experts through our white papers, providing valuable knowledge and analysis.
Our products solve everyday industrial communication problems. Discover how our customers have improved their business with HMS case studies.
HMS communication solutions help thousands of companies solve specific communication problems in many different industries and applications.