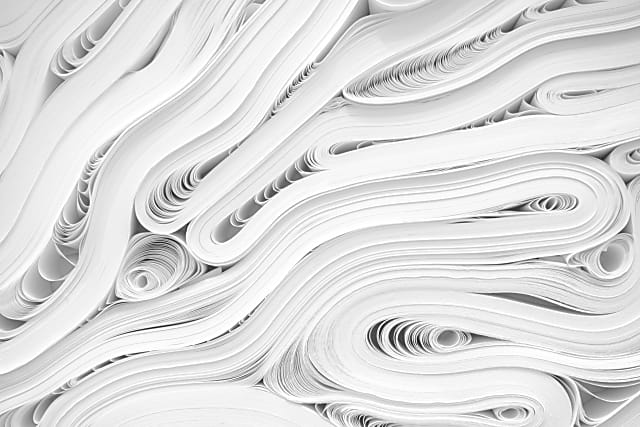
White papers
Stay up to date on the latest topics and gain industry insights from HMS' experts through our white papers, providing valuable knowledge and analysis.
Natgraph uses Ewon Flexy to monitor and control the production of polymer electrolyte membranes for fuel cells. The system enables precise temperature control, remote monitoring, and data security in a clean room environment, ensuring high-quality production.
Fuel cells are fast becoming a keystone technology in the drive for a cleaner, greener world free from global warming. Some of the most brilliant minds in production engineering are now focusing on making their manufacture fast, efficient, reliable and scalable. UK-based Natgraph is using Ewon Flexy to ensure constant optimization of the most critical stage of the process.
Fuel cells convert chemical energy into electrical power, operating efficiently and without harmful by-products that pollute the environment or cause global warming. Typically running on clean, abundant, naturally occurring hydrogen they combine this with atmospheric oxygen to create power, pure water and nothing else.
Developed to power spacecraft, an early fuel cell was instrumental in Apollo 13’s survival after a major systems malfunction. Fifty years on and they are used in every thing from tiny laptops to utility scale power plants, in electric vehicles and transportation, industrial production, commercial and residential buildings and as energy storage within power supply grids.
Having no moving parts, they are highly efficient, almost silent and produce zero or near-zero harmful emissions such as the greenhouse gas carbon dioxide.
They use internal anodes and cathodes to split hydrogen (or other fuel) atoms into protons and neutrons and separate these through a PEM (polymer electrolyte membrane, also called a proton exchange membrane) to create a flow of electrical power. The PEM looks about as exciting than kitchen shrink wrap, but in fact is seven layers or precision made sophistication – and that is where Natgraph comes in!
Natgraph has spent the whole of its 40 year history at the cutting edge of drying and curing technology. Starting in high speed print works, it soon shifted focus to industrial applications with their requirements for constantly improving precision and control, uniformity and repeatability. Today it is the drying supplier of choice in the Automotive, Medical, Electronics, Security Print, Glass, Label, Textile Transfer and Print Finishing markets and works with clients to constantly improve and advance their critical processes.
Chief Engineer, Darren Kerry explains: “Our clients often require tailored, high-performance solutions and so our factory is designed for that very purpose. We are vertically integrated so that we can quickly and efficiently produce bespoke precise, controllable and energy efficient electro-mechanical drying equipment. We are agile, responsive and innovative and have the single aim of supplying the best kit available anywhere in the world.
“We have enviable track records for producing highly innovative drying and curing solutions based on convection, infrared and ultraviolet drying technologies, so can meet the needs of any project. So when we were approached to help scale up fuel cell production, specifically on PEM manufacture, we were quickly able to identify optimum solutions.”
A PEM consists of seven separate layers of membrane, each one individually layered onto a polyester backing sheet and precision cured before the next is applied. Once all seven are cured the backing sheet is peeled away and a final curing homogenizes the layers to fuses them into one.
The curing temperatures have to be exact across every millimeter of each layer and the end result is a very high value product, so wastage has to be avoided at all costs.
“To add to the jeopardy, its a reel to reel process, with each production run being over a kilometer long,” says Darren, “so scrapage is not really an option on this process. Its 100% accuracy at all times!” To add to this, production has to take place in clean room conditions and the whole production plant is a high security site to protect both the client’s valuable trade secrets and the costly materials used in the process. Part of Natgraph’s brief was to develop a secure communication system that allowed the drying and curing plant to be remotely monitored, adjusted, reset and optimised so that personnel did not have to constantly enter the high security cleanroom and which kept all data safe from cyberattack or cybertheft. To this end it developed a VPN (virtual private network) based on Ewon Flexy technology from HMS Industrial Networks.
Using Ewon Flexy we have developed a world-class control and monitoring system that only authorised personnel can access.
Darren Kerry, Chief Engineer, Natgraph Ltd
The Ewon Flexy is an IIoT data gateway with VPN connectivity, which has enabled Natgraph to configure a multi-purpose internet data gateway so that it can monitor and collect vital key performance indicators (KPIs) for analysis and predictive maintenance. On-site data monitoring is available for all the major PLC protocols for data logging and alarm notification, while an OPC UA server shares data with the plant’s Enterprise Systems.
This information is also available securely to remote personnel through the Ewon Talk2m’s M2web service. Darren explains the system’s capabilities: “Continuous data logging and buffering can be performed on every tag-name. Ewon stores tag data values (+ timestamp) in its internal database for statistical analysis, trend identification and later review.”
The Datamailbox service of Talk2m is an online data buffer that allows the easy retrieval of data. As such we can monitor the performance of the PEM production line in real time, log the data for long term analysis and reset or optimize the process remotely. This means we do not have to enter the clean room environment or go through the plant’s on-site security protocols.
“All the communications are to VPN standards, so data is secure and confidentiality is maintained.”
Stay up to date on the latest topics and gain industry insights from HMS' experts through our white papers, providing valuable knowledge and analysis.
Our products solve everyday industrial communication problems. Discover how our customers have improved their business with HMS case studies.
HMS communication solutions help thousands of companies solve specific communication problems in many different industries and applications.