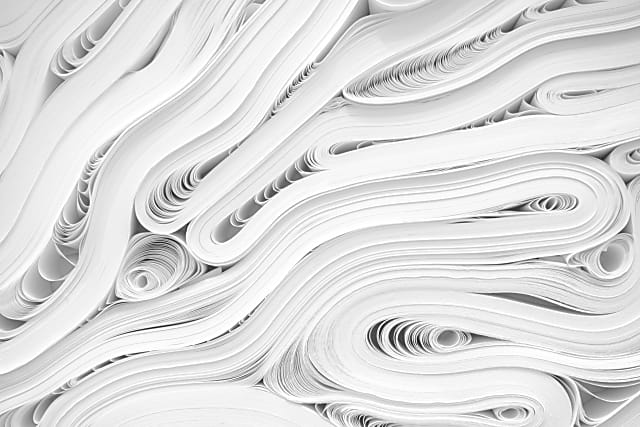
White papers
Stay up to date on the latest topics and gain industry insights from HMS' experts through our white papers, providing valuable knowledge and analysis.
ETAS uses Ixxat PC CAN interfaces to enable communication between their LABCAR HiL test system and different Electronic Control Units (ECUs).
ETAS GmbH in Germany is well-known in the automotive business for their LABCAR solution – a powerful test system that simulates the behavior of a car, enabling users to test brakes, gearboxes, speed controls, and other electronic car systems in a controlled environment. ETAS is using Ixxat PC CAN interface boards for connectivity to the CAN and LIN buses used by the car systems.
A modern car is more or less a computer system on wheels. Not only do you have computers running the actual powertrain (the engine, gearbox, and other components used to propel the car forward), but computers also control the dashboard, air-conditioning, parking system, speed control, immobilizer, entertainment system, and so on.
These computers throughout the car are called Electronic Control Units or ECUs. Since it is of utmost importance that ECUs work as intended, they are thoroughly tested before being put into serial production. Testing of the ECU software is usually done using so called Hardware-in-the-Loop (HiL) systems allowing users to test the ECUs in a lab environment.
We have not had a single quality issue with the Ixxat PC CAN interfaces in ten years, which is good proof of the quality we expect and that we deliver to our customers.
Henrik Jakoby, Product Manager, ETAS
LABCAR from ETAS GmbH is one of the technically leading HiL-solutions with the ability to simulate any part of a car. This allows users to observe and measure the ECUs’ response in absence of a physical vehicle. LABCAR is used for simulating both normal operation as well as critical behavior – for example injecting invalid data signals.
ETAS is a subsidiary of Bosch headquartered in Stuttgart, Germany. They provide innovative solutions for embedded systems and are trusted by many of the world’s major car and ECU manufacturers.
LABCAR is a complete solution including a real-time PC as well as the software which enables the simulation. To communicate with the ECUs, the PC needs access to analog and digital I/Os as well as the networks used by the different ECUs. CAN and LIN are the most important standards for in-vehicle communication. To connect the PC to these networks, ETAS is using Ixxat PC CAN interface cards with the related Ixxat LINUX-drivers.
“We found the Ixxat PC CAN interfaces many years ago when looking for a solution to connect the ECUs to the LABCAR,” says Henrik Jakoby, Product Manager at ETAS. “What we really appreciated about the Ixxat solutions was that they had a really easy-to-use and powerful API that could be used in our software.”
After implementing the first Ixxat PC CAN interfaces in 2004, the cooperation between ETAS and HMS has become more of a partnership where a lot of requirements from ETAS have been implemented into the standard Ixxat offering, including special driver features like “single shot mode.”
“We have a very close collaboration with the Ixxat team at HMS,” says Henrik Jakoby. “The technical support has been very good and our engineers are in contact on a regular basis to solve connectivity issues.”
Example of a test dashboard in the LABCAR user interface.
Flexible and fast connectivity between test systems and Devices Under Tests (DUTs) is very important in automotive testing. For example, connectivity to the LIN bus is a growing demand. LIN is more cost-efficient than CAN due to cheap cabling and low system requirements. As opposed to digital and analog lines, it is also possible to do diagnosis via the LIN bus. Originally intended for comfort functions like power windows, LIN is now being deployed in more and more systems including powertrain.
To enable ETAS to provide the best solution to their customers, each Ixxat CAN-IB200/PCIe interface provides up to four LIN-ports in addition to CAN.
Another challenge is speed. The communication between the ECU and the LABCAR puts high demands on low latency in combination with high data rate communication. This is especially important since a LABCAR computer may be connected to several ECUs with multiple network interfaces.
The Ixxat CAN-IB200/PCIe solves this through the expansion board, providing 4 high-speed CAN ports per PCIe slot, enabling up to 32 CAN ports per PC. The design of the CAN-IB200/PCIe with a powerful 32 bit CPU buffer as well as a sophisticated driver architecture keep the PC-load for communication as low as possible in order to maximize the performance of the simulation.
“All in all, we are very satisfied with the Ixxat PC CAN interfaces and the support we get,” says Henrik Jakoby. “Indeed, we have not had a single quality issue with the Ixxat PC CAN interfaces in ten years, which is good proof of the quality we expect and that we deliver to our customers.”
Company: ETAS GmbH
Country: Germany
Solution: Ixxat PC interfaces
Industries: Automotive testing
Products: Ixxat CAN-IB 200/PCIe
Stay up to date on the latest topics and gain industry insights from HMS' experts through our white papers, providing valuable knowledge and analysis.
Our products solve everyday industrial communication problems. Discover how our customers have improved their business with HMS case studies.
HMS communication solutions help thousands of companies solve specific communication problems in many different industries and applications.