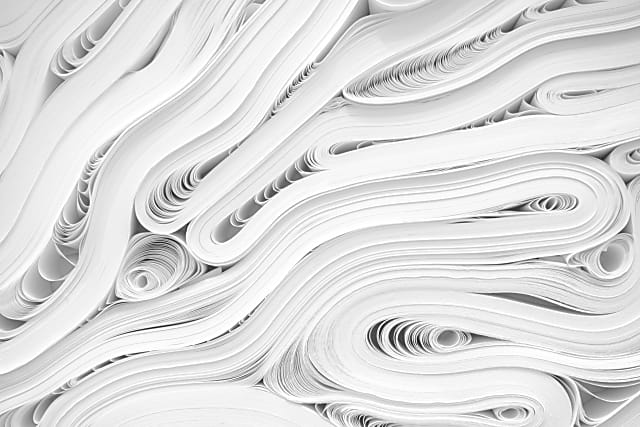
White papers
Stay up to date on the latest topics and gain industry insights from HMS' experts through our white papers, providing valuable knowledge and analysis.
Palfinger AG uses CAN communication solutions from HMS Networks to ensure safe, efficient, and reliable lifting equipment for rail vehicles. The CANbridge NT 200 filters and stabilizes communication, preventing overload and errors.
Connecting equipment to vehicle bus with data filtering
Background
Safety, efficiency, and reliability are among the key requirements for lifting equipment on rail vehicles. Stable data communication in the system connecting the rail vehicle with the lifting equipment is an important prerequisite for meeting these requirements. Palfinger AG, an Austrian machinery company, is a world leader in hydraulic cranes and lifting equipment. It uses CAN communication solutions from HMS Networks to avoid multiple technical issues in all of its model lines.
Rail networks worldwide are expensive to build, maintain, and repair. Palfinger’s lifting equipment for rail vehicles is developed for precisely these purposes, so it must be able to perform different tasks including precision work on overhead line systems; construction, repair and maintenance tasks; bridge inspections; and positioning suspension ropes. The rail vehicles used for such activities need special auxiliary equipment such as cranes, aerial work platforms, or remote-controlled positioning and cantilever units.
A crucial benefit for us is that the CANbridge works reliably on both sides even at different baud rates, so it serves as a stabilizing element.
Stephan Fischhofer, Software development team leader, Special Solutions, Palfinger AG
Since 2008, most of Palfinger’s railway systems have been equipped with the Paltronic 150 system for controlling the communication between rail vehicles and Palfinger’s systems. The Paltronic system enables data to be exchanged via CAN bus between the vehicle control system and the lifting equipment’s control units. “The main problem for us with this switchover was that the CAN data traffic between the systems needed to be reduced to essentials to avoid control system overload and communication errors,” said Stephan Fischhofer, software development team leader for special solutions at Palfinger. “In the end, this communication has to be completely safe and reliable to protect both the machinery and its users.” The vehicle control systems often sent messages that were irrelevant for Palfinger’s equipment, and vice versa. In addition, the developers were confronted with the situation that the different CAN buses worked with different baud rates, making it impossible to ensure smooth communication.
To overcome these challenges, Palfinger chose the CANbridge NT 200. It filters the CAN message traffic between vehicles and Palfinger equipment so that the different target systems only receive relevant messages. “The CANbridge ensures that vehicle data that aren’t important for Palfinger equipment don’t reach that equipment, and that only relevant Palfinger-specific data get sent to the vehicle control systems,” Fischhofer said. “Another crucial benefit for us is that the CANbridge works reliably on both sides even at different baud rates, so it serves as a stabilizing element.” This approach made it possible to efficiently overcome technical communication problems between vehicles and lifting equipment while ensuring that there are no communication errors even with differently configured CAN networks.
The CANbridge NT 200 model is a versatile communications module specially developed to filter and convert CAN messages. It enables the connection of CAN systems with different baud rates and features flexible filtering and mapping functionality. It can be configured with user-friendly Windows software so users can set precise filtering rules. The CANbridge NT 200 can also be used as a protocol converter to transfer data from one CAN network to another. With this solution, Palfinger can efficiently control the communication between its railway equipment and the vehicle control systems while ensuring a high degree of system stability.
Country: Austria
Solution: CAN network gateways
Industry: Railway cranes
Product: CANbridge NT 200
Stay up to date on the latest topics and gain industry insights from HMS' experts through our white papers, providing valuable knowledge and analysis.
Our products solve everyday industrial communication problems. Discover how our customers have improved their business with HMS case studies.
HMS communication solutions help thousands of companies solve specific communication problems in many different industries and applications.