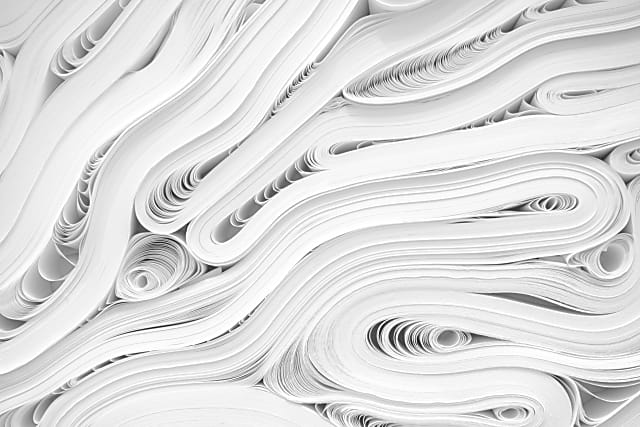
White papers
Stay up to date on the latest topics and gain industry insights from HMS' experts through our white papers, providing valuable knowledge and analysis.
Reinova S.p.a, especially its Reitech subdivision, is a leading automotive testing house in Italy’s “Motor Valley,” focusing on electric mobility and batteries. They use the CANnector platform from Ixxat to ensure reliable and flexible test lab communication between test bench automation and in-vehicle networks (IVNs).
In automotive testing, especially in the area of e-mobility, time and system flexibility are king. The design validation (DV) of ev components such as Battery Packs, Modules, Cells, DC/DC Converters, e-Motors, need to meet the high quality standards and safety regulations put to the industry. In order to fulfill these requirements, the communication from test bench automation and the in-vehicle networks (IVNs) needs to offer a maximum of reliability, performance, useability and system flexibility. The Italian testing expert and innovation leader Reinova S.p.a therefore relies on the automotive all-in-one platform CANnector from Ixxat.
As a strong business unit within Reinova, the Reitech subdivision has grown a profound reputation in Italy as a well-known automotive testing house in “The Motor Valley” and far beyond partnering with one of the world’s most premium and luxury supercar brands. Providing certification tests and product development for its customers, they cover different testing laboratories such as EMC or RED, focusing on the electric mobility market, especially on batteries.
With the CANnector, there’s no need for time-consuming programming effort, only easy parameterization needs to be done – saving time and money.
Marco Rotella - Chief Digital Officer from Reinova
Different automotive testing scopes and kinds of DUTs (devices under test) from various OEMs require flexible hardware and software solutions for the communication between the DUTs and the test automation system inside the climate test chambers. These solutions must be flexible, easy-to-configure and robust - not consuming much time setting them up and operating them. The variety of different DUTs such as battery packs and cells, BMS, inverters, e-Motors and many other electric components even puts a higher request to the interfaces – in terms of EMC immunity, uptime and reliability. Not only in the final test operation, but also during the development phase of the applications, a flexible and easy-to-use communication interface is crucial. “By using the ACT software we’re able to quickly reconfigure devices in order to vary the signals exchanged between the DUT and the automation system, adapting to prototypes development”, explains Chief Digital Officer Marco Rotella from Reitech.
Control cabinet for automotive testing with Ixxat CANnector devices inside.
In their automotive testing house, Reinova Labs counts on the Beckhoff automation system TwinCAT using the EtherCAT protocol to control the whole test bench, whereas most of the DUTs typically are based on CAN, CAN FD or LIN. In order to connect both worlds, the CANnector LE in between has been used as a CAN and LIN to EtherCAT gateway in one of their first projects. But depending on their customers’ requests and the parameters to be validated, the system setup inside the climate chambers, the configuration, the needed connectors and the needed protocols differ. Luckily, CANnector provides not only a pure gateway functionality, but also can run specific applications such as converting on-the-fly IVN (in-vehicle networks) signals (e. g. DBC, ARXML, etc.) into EtherCAT objects. As a standalone device, it is directly connected to the DUT and the EtherCAT master - not needing an additional PC. As well, fieldbus length limitations or EMC interferences can be erased and surrounding assets can be protected from high voltages. “HMS allows us to extend the functionalities of a PLC connecting it with the automotive world’s field buses. With the CANnector, there’s no need for time-consuming programming effort, only easy parameterization needs to be done – saving time and money“, adds Rotella.
System overview
The robust aluminum housing is ideally suited for any industrial use. The Linux-based embedded platform covering CAN, CAN FD, LIN and FlexRay comes along with the PC-based engineering tool ACT (Advanced Configuration Tool) ensuring easy configuration and useability. Four D-Sub9 connectors provide up to eight separate CAN channels – simplifying the integration of many bus systems at once. Two USB A and one mini-USB connector along with three RJ45 connectors (1 x Ethernet, 2 x EtherCAT) ensure a fast and reliable communication between in-vehicle network, automation system and PC configuration tool. This altogether results in an optimized standalone solution saving time and money for the customer.
Country: Italy
Company: Reinova S.p.a.
Solution: Automotive gateway
Industries: Automotive testing
Products: Embedded Platform CANnector LE
Stay up to date on the latest topics and gain industry insights from HMS' experts through our white papers, providing valuable knowledge and analysis.
Our products solve everyday industrial communication problems. Discover how our customers have improved their business with HMS case studies.
HMS communication solutions help thousands of companies solve specific communication problems in many different industries and applications.