This article provides a guide for setting up and configuring the CM CANopen Module, which allows system integrators to connect CANopen or CAN 2.0A devices to a SIMATIC S7-1200 PLC. The module seamlessly integrates into the SIMATIC environment, enabling the use of a wide range of CAN-based devices in automation systems. The article includes a video tutorial that walks through the configuration process using the TIA Portal and the CM CANopen Configuration Studio.
APPLICABLE PRODUCTS
Ixxat CM CANopen Module
ISSUE / QUESTION / SYMPTOM
How do I set up and configure the Ixxat CM CANopen Module with a SIMATIC S7-1200 PLC?
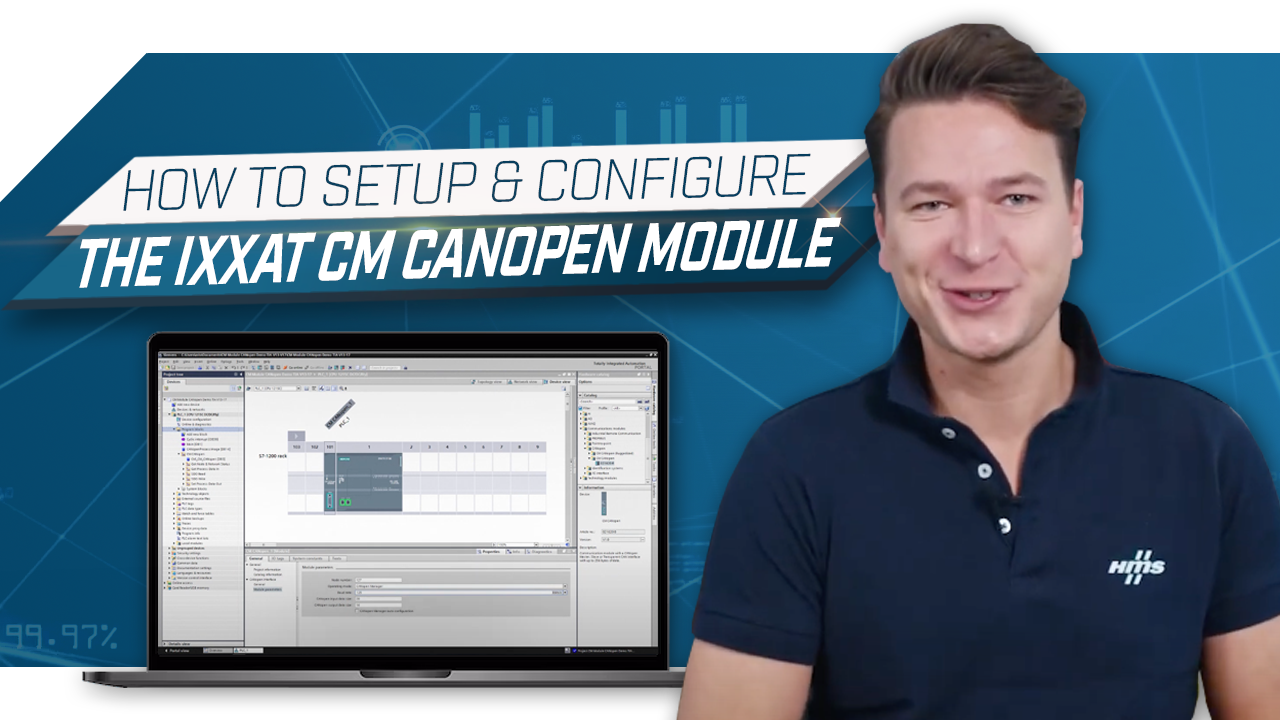
Watch the video to learn more...
The CM CANopen Module enables system integrators to connect CANopen or CAN 2.0A devices to a SIMATIC S7-1200 PLC, providing greater flexibility in automation system design. Below are the key steps to set up and configure the CM CANopen module:
1. CM CANopen Module Setup:
The CM CANopen module plugs into the communication module interface of the S7-1200 PLC. This establishes the hardware connection between the PLC and the CANopen or CAN 2.0A devices.
2. Configuration Using TIA Portal:
The configuration of the module is performed using TIA Portal, Siemens' engineering framework. The CM CANopen module integrates seamlessly into the TIA Portal, where the user can configure the module as part of the overall automation project.
3. CANopen Network Configuration via CM CANopen Configuration Studio:
The CM CANopen Configuration Studio is a free tool provided by Ixxat to easily configure the connected CANopen network. This software allows you to set up CANopen devices, define communication parameters, and map data objects (PDOs).
4. Verification of PDO Mapping:
After setting up the network, it’s essential to verify the PDO (Process Data Object) mapping to ensure correct data exchange between the CANopen devices and the PLC. This step ensures that the communication configuration is correct and that data is being transmitted and received as expected.